Right, let’s talk about this Maestrelli business. It wasn’t something I planned, you know? Just sort of happened. I was clearing out the old shed, place hadn’t been touched in years, and buried under a pile of junk, there it was. This old, dusty Maestrelli thing. Looked like some kind of specialised press or clamp, heavy as anything. Didn’t even know we had it.
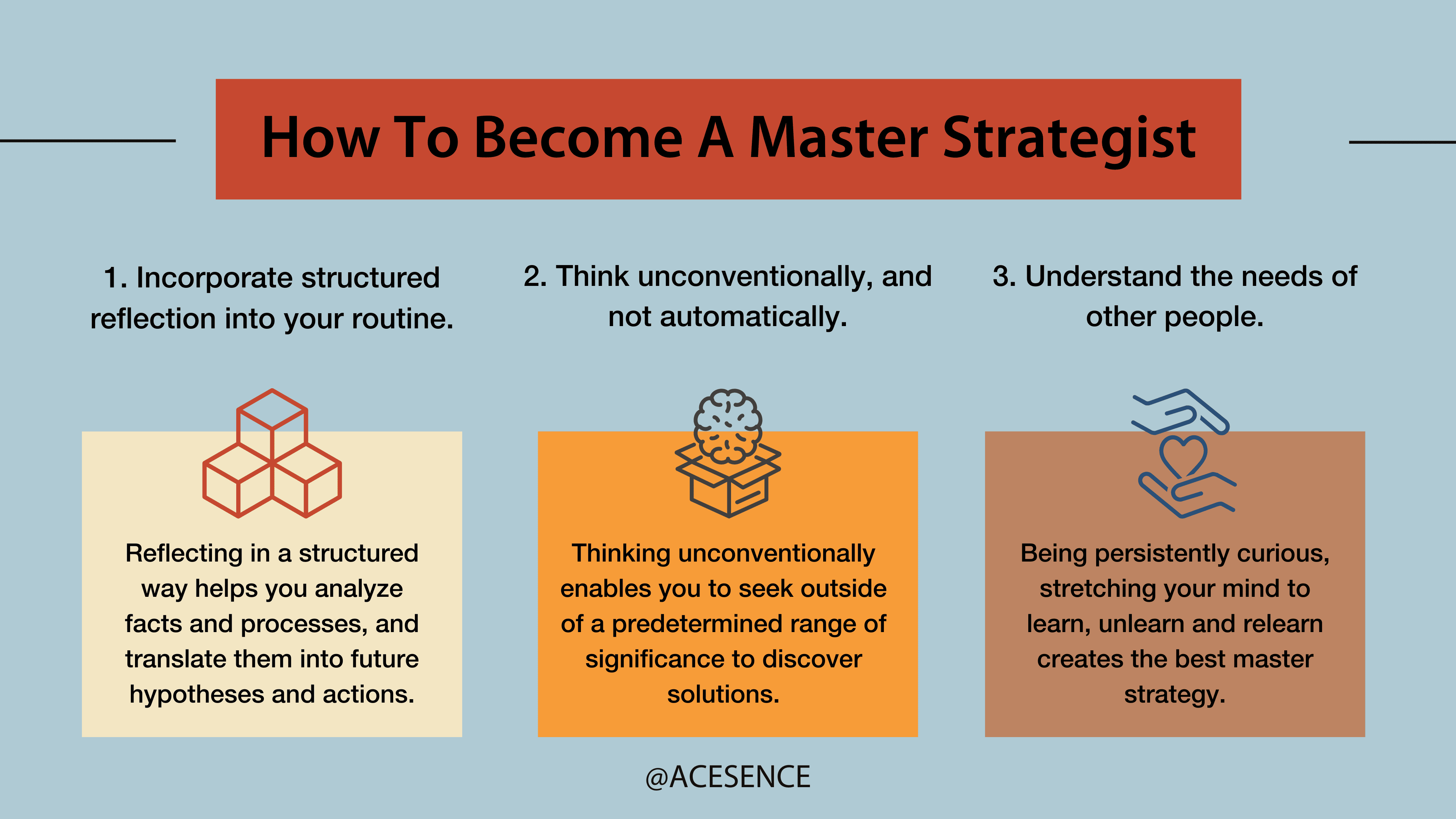
Getting Started
First thing was just dragging it out into the light. Caked in grime. Looked like it hadn’t moved since the dinosaurs. My first thought was, “scrap metal”. But then, I don’t know, curiosity got the better of me. It had this solid feel, you know? Not like the flimsy stuff you buy today. So, I decided, what the heck, let’s see if I can get it working.
Cleaning was the first real job. Took ages. Used wire brushes, degreaser, rags, the whole nine yards. Underneath all the gunk, the actual metalwork was surprisingly okay. Some surface rust, but nothing too deep. The moving parts, though, were seized up solid.
The Actual Work
This is where the fun started. Or the frustration, depending on how you look at it.
- Disassembly: Had to figure out how the thing even came apart. No manual, obviously. Just brute force and guesswork. Lots of tapping with a mallet, soaking bolts in penetrating oil overnight. One particularly stubborn bolt just wouldn’t budge. Spent a whole afternoon on that one stupid bolt. Nearly threw the whole thing across the yard.
- Finding Parts: Once I got it in pieces, I could see what needed replacing. A couple of bushings were shot, and some kind of spring mechanism looked dodgy. Finding replacements? Forget about it. Maestrelli, whoever they were, clearly weren’t making parts for this ancient beast anymore. Ended up having to measure the old bits really carefully and then spend hours online trying to find something generic that might fit. Total pain. Found some bushings that were close and had to modify them with a file. Not ideal, but what else could I do?
- Putting it Back Together: Reassembly was mostly okay, just the reverse of taking it apart. But lining everything up perfectly was tricky. That spring mechanism I mentioned? Absolute nightmare. Kept pinging off. Nearly lost an eye. Had to get my neighbour to give me a hand just to hold it in place while I secured it.
The Result
So, after all that messing about, did it work? Yeah, surprisingly, it did. The main lever moves smoothly now, the clamping action feels solid. It actually functions like it’s supposed to. I haven’t actually used it for a real project yet, mind you. Still trying to figure out what its original purpose even was! Looks like it might be good for some leatherworking or maybe bookbinding? Who knows.
Was it worth it? Probably not, if you count the hours I sank into it. Could have bought something modern for less hassle. But there’s a certain satisfaction, you know? Taking this old, forgotten lump of metal and bringing it back to life. It’s got character. And honestly, it was something to do. Kept me busy when everything else felt a bit slow.
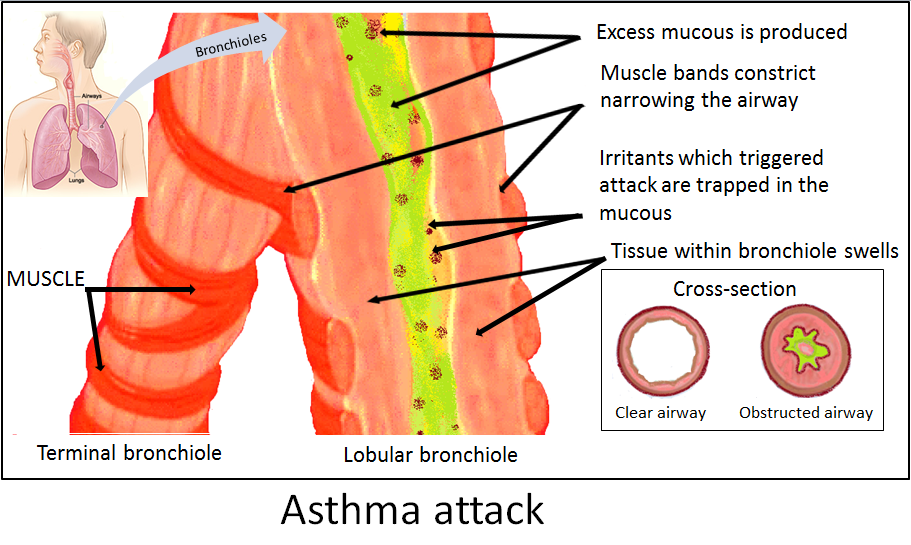
So yeah, that was my adventure with the Maestrelli mystery tool. A lot of work for an uncertain reward, but sometimes that’s just how these projects go. Made me appreciate modern tools a bit more, but also respect how things used to be built. Solid stuff, even if it’s a pain to fix.